Mold Design--- |
At the
starting point of the process, we can either follow the 2D
drawings or sketches from customers, or re-engineering existing
models to capture the required data for constructing a 3D solid
model for the project. According as the customer's requirements,
We utilize Pro/Engineer to build the model for different
applications. Upon approval of the design appearance, we proceed
to 'breaking-up' the outlook model into different parts and
continue the assembly design of both internal and external
components. Customer's requirements are inputs for the process.
We capture the idea and design given and construct the 'real'
model that match customers ideas digitally |
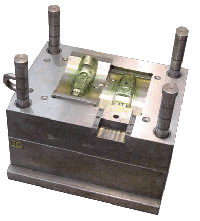
CAD/CAM DESIGN |
Product Development--- |
We are capable of providing reverse engineering
and concurrent engineering to our customers. Our specialty in
offering "Total Solution" service with the integration of our
mold tooling and plastic injection capabilities enable our
manufacture of custom-made molds to plastic products in an
efficient, effective and economical manner. |
Reverse Engineering--- |
We work actively and closely with our customers
in developing engineering models and products from existing
parts or tools, that is a "reverse" of the normal engineering
process which works out the design of the products first and
then identifies the necessary parts or tools. We are equipped
with advanced Pro/Engineer and other CAD/CAM/CAE systems for
working out the conceptual idea of a mold to its actual
production within a very short span of time. |
Concurrent Engineering--- |
For the manufacture of molds, designing and
developing new products is becoming a bottleneck of the whole
product development cycle and consumes much of the production
time. By using the specialized technique, Pro/Engineer,
CAD/CAM/CAE equipment and production process simulation, we are
able to close the gap between the design terms and production,
and to achieve a faster moving product cycle. In general, this
is known as concurrent engineering. Communication time as well
as the overall inertia of the project is thus minimized. In
addition, any design modifications or corrections to flaws can
be made possible in the very early stages with the digital
simulation during the process. Customers, hence, achieve
substantial savings on both their product development time and
costs. |
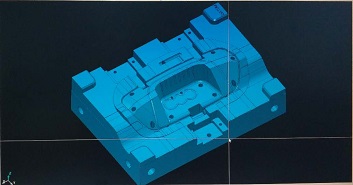
|
|
|